News
better business decisions
Posted 6 years ago | 6 minute read
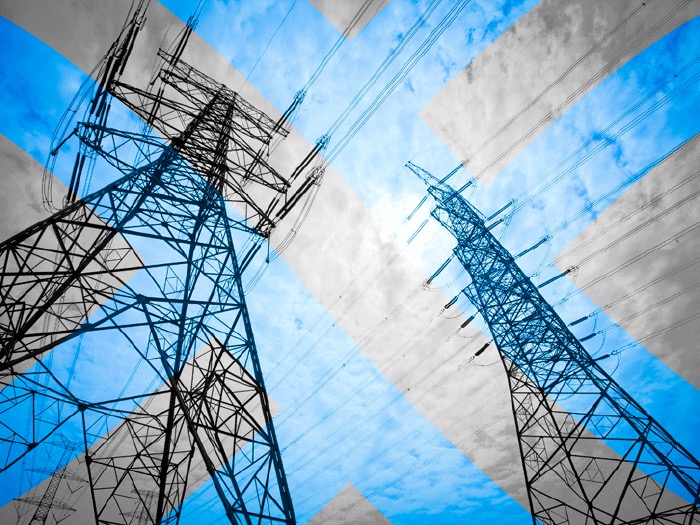
DSR: The Future of Energy is Convergence
Traditional demand side response (DSR) is converging with enhanced energy and operational services. Balancing services markets are moving closer to the time of use (for example the recent launch of the weekly FFR auctions), energy trading is starting to take off, and operations are increasingly part of the puzzle in creating the most efficient and cost effective business cases. As automation is increasingly prevalent in all areas of industry, energy technology needs to be more sophisticated, cover more ground, and take into consideration the interoperability of every area of business.
Energy Markets & Zero-Carbon Targets
We’ve come a long way since the emergence of peak avoidance schemes, the slow-reacting STOR markets and the introduction of energy efficiency and reduction programmes. I&C have needed to keep costs down to stay in line with highly competitive markets, and the grid has needed to keep up with rising renewable generation.

The UK’s targets to decarbonise, decentralise and digitalise greatly affect industry. New net-zero carbon legislation means that there will be little choice but to comply with new emission reduction programmes. Whilst many companies are already participating in some form of DSR, the drastic changes to the grid and to national policy mean there are new ways for large-scale industrial and commercial businesses to participate in energy markets. But how can these be amalgamated and combined with wider energy and operational strategies?
Not all DSR technology is created equal. Very few technology providers combine DSR with energy and operational services such as scheduling automations, energy monitoring and metering, trading, storage management, asset efficiency automations, production efficiency automations, predictive maintenance, fault-finding, analytics, reporting and more. I&C want more from their providers, and the convergence of energy related services as a whole has been a trend in 2019. Just look at the partnerships being formed between suppliers and DSR technology providers (GridBeyond recently partnered with business energy supplier Haven, and the construction and maintenance arm of the DNO Electricity North West).
So what is meant by energy services?
Energy services is a broad term, but is widely known as the additional energy related services that can be leveraged using energy technology. Common services are metering, energy analytics, trading, compliance services and demand side response.
The services that can be delivered and the efficiencies and savings that can be accessed are dependent upon the sophistication of the technology, and the company delivering the services.
Energy services are more than a product, and supersede hardware or software. For optimised results, energy services typically require a consultative approach from a provider, such as GridBeyond. The team behind the technology should be able to a create bespoke energy services plan for your business, and deliver human expertise alongside the technology deliverables.
Optimising Operations with Energy Services
Operations are the core of every business (obviously), and any projects that have the ability to affect production or processes are often heavily scrutinised. This usually includes energy related projects. But what if energy services could actually enhance operations?
Energy consumption data can tell us a lot about the health of an asset. By understanding the regular patterns of consumption, and adding this to scheduling or processing data, anomalies can be recognised and, with technology such as GridBeyond’s, can be automatically acted upon and efficiencies created.
By using energy monitoring to identify patterns, businesses can proactively plan to avoid and mitigate the risks associated with planned and unplanned maintenance as well as improve scheduling efficiencies and hit KPIs.
Examples of Asset Level Fault-Finding & Preventative Maintenance
By measuring the energy consumption of an asset, we can build a complex energy profile. By collating this data, and combining aggregated data from similar assets, our machine learning technology identifies patterns and decides whether there is a risk that the asset will fail, and provide alerts accordingly.
By ascertaining the likelihood of a fault occurring, businesses can save significantly.
A fault detected early results in approximately £8k in maintenance costs and production loss, whereas reactive maintenance can cost around £48k. That’s a 500% difference in costs.

Improved Efficiencies
There are limited efficiency successes to be had once all the lightbulbs have been swapped for energy efficient ones, the air conditioning has been fine tuned to its optimum output, your equipment has been retrofitted with the latest energy efficient version, and you’ve implemented your “switch off” policy. These programmes are relatively static.
By connecting your assets to advanced monitoring systems, machine learning algorithms find patterns in consumption which form the basis for efficiency and maintenance profiles. By ascertaining energy flexibility, equipment can be more energy efficient, and by ascertaining production and processing schedules, operational efficiencies can be created and savings optimised.
For example, GridBeyond works with refrigeration plants to install additional smart sensors to ascertain the cost incurred every time a fridge or freezer door is opened. The platform then uses that data, plus scheduling and forecasted energy costs, to work out how to most efficiently operate. These decisions are made within split seconds and are immediately, automatically acted upon.
Automation & Digitalisation: Industry 4.0
Engagement in the automation and digitalisation involved in the Industry 4.0 movement is now a necessity for industrial and commercial sites. With that, the measurement, monitoring, automation and control of energy are imperative to streamlining and optimising processes, as well as enhancing profitability and sustainability.
The patterns emerging from machine learning technologies are used to improve on-site overall equipment effectiveness (OEE) and predictive maintenance. Predictive maintenance is often overlooked but is becoming more prevalent from a financial and operational planning perspective, as well as ensuring further business resilience. It ensures adequate visibility to take action and provides the automation, alerts and thresholds required before a key process fails. The data gathered from a connected network of assets means highly accurate automation in this sense, as well as key insights for benchmarking and analytics.
The interoperability of machines, devices, sensors (and humans for that matter) is unavoidable in every area of industry. Energy and operations are no different. From m2m communication, to artificial intelligence, machine learning and big data, the connected organisation is here.
In summary…
High-end technology platforms enable automated participation in the most valuable demand side response programmes and avoid peak electricity charges, integrating seamlessly with and enhancing the overall energy strategy. By boosting energy performance and implementing automations and alerts for operational optimisation, an industrial site becomes financially and operationally more resilient.
Energy and operations are intrinsically linked. To maximise one, the other must integrate.