News
better business decisions
Posted 1 year ago | 4 minute read
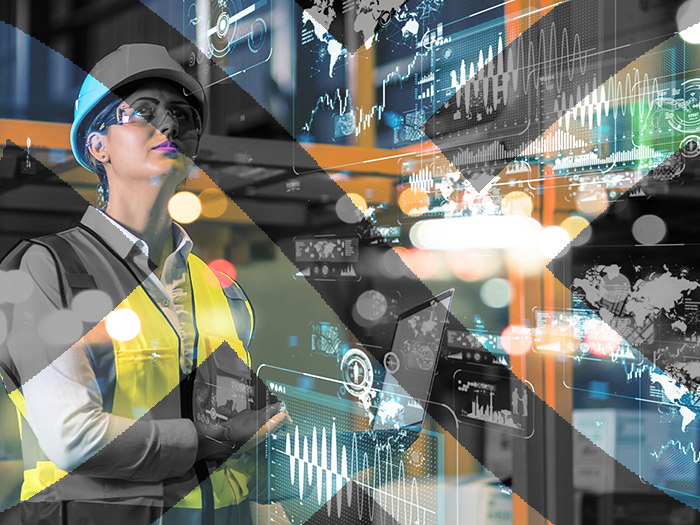
Intelligent demand side response | The power of digital twins
In the dynamic landscape of industrial energy management, businesses are increasingly turning to cutting-edge technologies to optimise their operations. One such revolutionary tool gaining prominence is the use of digital twins to model energy demand, generation, and storage.
Digital twins are already being used to model many different things, from car engines, to supply chains, to entire cities and are increasingly being used to gain insights into energy systems. But what are digital twins, and why do they matter?
What are digital twins?
Digital twins are defined by techUK as “a relevant, virtual representation of the state and behaviour of something physical or non-physical with a functional output in the real world”. Essentially a digital twin is a digital – and often real-time – copy of a real-life asset, process, or system. They allow stakeholders and policy-makers to gain insights into processes that would be otherwise highly time and labour intensive.
Drawing on inputs and data from multiple sensors, digital twins are helping to expose gaps and relationships between plans, actions, and possible outcomes, supporting multi-criteria decision-making and enabling users to test and model options and trade-offs. They can be used throughout the product lifecycle to simulate, predict, and optimize a product or process before anything ever goes into production.
How do digital twins work?
Digital twins use data from sensors installed on physical objects to determine the objects’ real-time performance, operating conditions and changes over time. For example, assets can be equipped with various sensors to produce data about different conditions of its performance. This data can include the object’s temperature, product output and environmental surroundings. The data is then processed through a system of computers and servers and applied to its virtual twin or counterpart. With an updated virtual model, operators can run simulations, analyse performance and discover potential areas of improvement. They can then apply this knowledge to the original physical object to optimise its performance.
Digital twin technology can also capture and monitor the real-time state of a physical object’s functions. This allows operators and engineers to predict how changing conditions will impact the object’s production or performance. With this information, they can answer the “what if” or “what will” questions about a plant, product or process. They also offer a way to stress-test important assets and systems in preparation for a wide range of scenarios, including severe weather episodes.
Precision analysis
Energy is a critical aspect of operations. Digital twins provide an unparalleled level of precision when it comes to analysing energy demand.
By creating a virtual replica of the entire site, every nuance of energy consumption is captured and scrutinised. Digital twins facilitate the creation of a comprehensive model that takes into account various factors affecting energy use, and therefore operating costs. This includes the integration of renewable, understanding peak demand periods, and strategically planning how demand, generation and storage assets can be best utilised to meet site requirements.
Tailored solutions
Digital twins also allow businesses to model and optimise storage solutions, whether they involve physical storage units like bins and hoppers, thermal storage in processes such as glass or steel production or power storage in the form of a battery.
One of the unique selling propositions of digital twins in energy management is their ability to maximize returns while respecting operational constraints. On sites where specific parameters must be adhered to, digital twins allow for a tailored approach. Businesses can achieve peak efficiency within their operational requirements, balancing profitability with efficient operations.
This precision allows businesses to identify real flexibility opportunities, enable more informed decision-making in optimising energy and creating a more efficient and cost-effective energy strategy.
Conclusion
The benefits of utilizing digital twins for modelling energy demand, generation, and storage are vast and transformative. From precision in demand analysis to strategic storage management and cost savings, the adoption of digital twins propels industrial energy management into a new era of efficiency and sustainability.
At GridBeyond we meticulously create a digital twin of your facility, gaining a granular understanding of your processes and unlocking hidden potential for demand flexibility. This enables:
- Real flexible load identification: Pinpointing the genuine flexibility in your energy consumption, we go beyond the surface, ensuring accurate insights into when and where adjustments can be made.
- Co-optimized trading strategy: Crafting a trading strategy that seamlessly optimizes your flexible load across all available markets. We ensure your participation is strategic, yielding maximum returns while adhering to operating requirements.